Our current production process for flanges mainly includes casting, forging, die forging, cutting, and other methods.
The production process for casting flanges is to melt the steel in a medium-frequency electric furnace to a temperature of 1600–1700 °C and then preheat the metal mold to 800-900 °C to maintain a constant temperature. Next, inject the molten steel into the preheated metal mold and wait for the casting flange to naturally cool to 800-900 °C for 1–10 minutes. Finally, cool it with water to nearly room temperature and remove the casting from the mold.
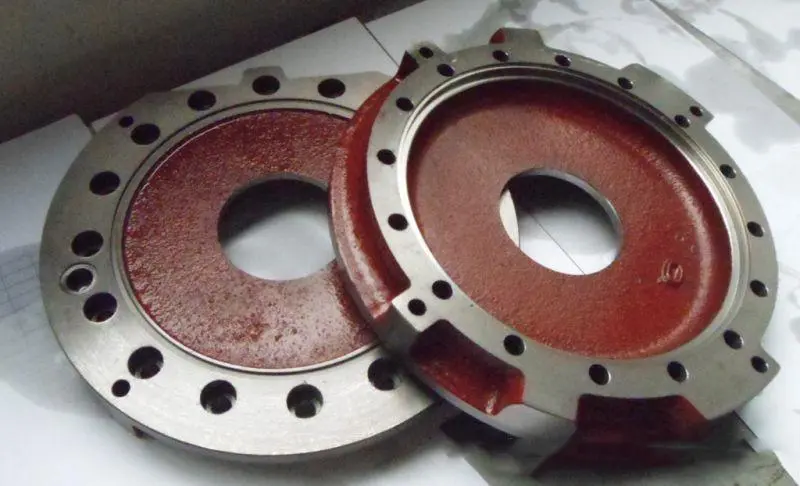
The production process of forging flanges involves the basic steps of selecting high-quality steel billets for cutting, heating, forming, and cooling after forging. The forging methods include free forging, die forging, and membrane forging. Among them are the high dimensional accuracy of the forged parts, the small machining allowance, and the more reasonable fiber structure distribution of the forged parts, which can further improve the parts’ service life.

Our company’s flange production process has its own characteristics, and how to choose the appropriate production process depends on the specific application requirements and product cost considerations. For example, the cost of casting flanges is relatively low, but there may be casting defects. For example, forging flanges have better shape and performance, but the cost is higher. Another advantage is that forged flanges have high precision and excellent performance, but the production process is relatively complex, and the production time may be longer. Large flanges, capable of producing a wider diameter range, typically employ cutting flanges in their production.
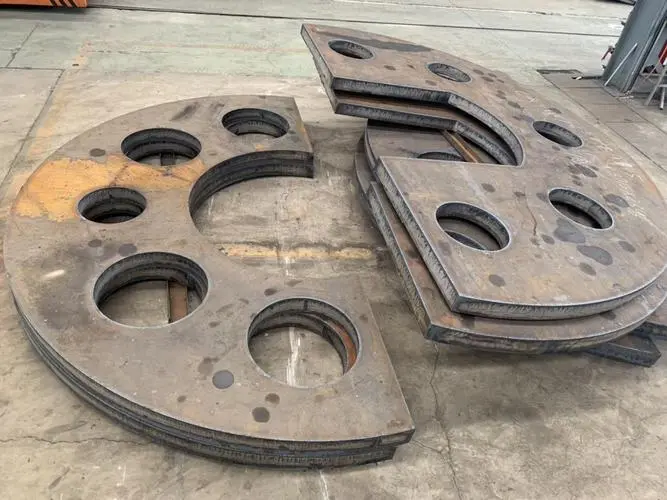