products
- Metal Casting (1)
- Metal Forging (1)
- Metal Laser Cutting (1)
- Metal Molds (1)
- Metal Surface Treatment (1)
- Uncategorized (24)
blogs
- P20 mold steel 2024 年 10 月 30 日
- Shell casting offers a number of important advantages. 2024 年 10 月 30 日
- D2 tool steelPerformance and Application of D2 Tool SteelD2 tool steel 2024 年 10 月 24 日
- Characteristics of AISI 4140 composite steel 2024 年 10 月 22 日
- Characteristics of SAE4340 steel 2024 年 10 月 22 日
Contact us for more information
Homogeneous armor steel
High-tech warfare is not the only form of warfare in use today. Army contact is also unavoidable. According to data, in the past two years, in addition to the original infantry tank coordination and special infiltration, the army has also adopted high-tech combat methods such as long-range drone bombing.
Nowadays, vehicles on the battlefield, including Jeeps, personnel carriers, anti-aircraft artillery vehicles, and other light transport units, must undergo external armor modification to increase soldiers’ survival rates. Armor cannot do without high-quality armor steel.
Various types of projectiles with varying distances and calibers, along with explosives, will impact armored steel during wartime use. Instantaneous armor steel can withstand tremendous kinetic energy, fragments, impacts, and energy gathering effects. Upon impact or bombing, armored steel will experience deformation, rupture, and even gasification. For this reason, we require armored steel to have extremely high ballistic resistance. Armour steel’s anti-ballistic performance is actually the ability to resist projectile penetration, impact, and collapse.
The anti-penetration capability refers to the maximum kinetic energy impact velocity at which the armor steel will not be penetrated under a certain thickness of armor steel and the angle of impact of the projectile.
Flanges have a function and purpose.
Flanges are important components commonly used in the modern mechanical industry, mainly for connecting pipelines. Many car modification enthusiasts actually enjoy adding flanges to their vehicles. Let’s look at the functions and uses of flanges together.
Firstly, the function of a car flange is to expand the wheelbase, which can improve the stability of the car’s quick cornering and reduce the car’s roll.
Secondly, the fenders recess most of the original car wheels. After adding flanges, car enthusiasts can make the wheels flush with the fenders, which makes the car look more visually appealing.
Thirdly, when modifying wheels, it is recommended that car enthusiasts do not seek cheap options to purchase counterfeit wheels; fake wheels may break during driving, which can affect driving safety.
Fourthly, rebalance each wheel after installing the tires onto the new wheel rims to avoid abnormal shaking while driving at high speeds.
Fifth: When using the car, it is necessary to regularly check the tire pressure and also frequently inspect the tire surface for any signs of damage.
Stainless steel flat welding flange
Flange connection is the process of fixing two pipes, fittings, or equipment onto a flange plate, adding flange pads between the two flanges, and fastening them together with bolts to complete the connection. Some pipe fittings and equipment already include flanges, which are also flange connections.
Everywhere in a boiler room or production site, there are flanged pipes and equipment.
The connection method divides flange connection types into the following categories: plate flat welding flange, neck flat welding flange, neck butt welding flange, socket welding flange, threaded flange, flange cover, neck butt welding ring loose sleeve flange, flat welding ring loose sleeve flange, ring groove surface flange and flange cover, large diameter flat plate flange, large diameter high neck flange, eight-shaped blind plate, butt welding ring loose sleeve flange, etc.
Scope of application
Due to their excellent comprehensive performance, flanges are widely used in basic engineering such as chemical, construction, water supply, drainage, petroleum, light and heavy industries, refrigeration, sanitation, plumbing, fire protection, power, aerospace, shipbuilding, etc.
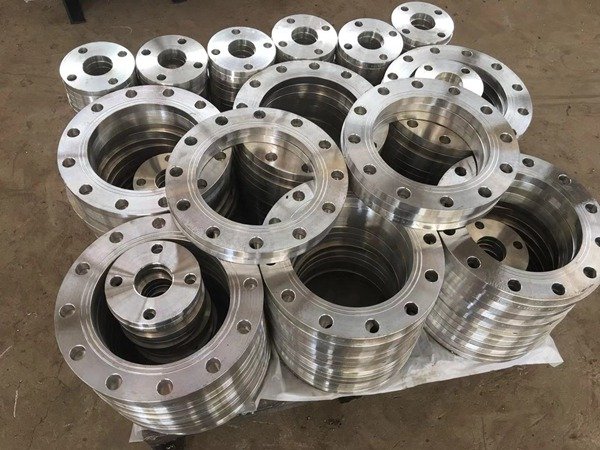
Marine steel plate
Our factory currently produces steel for shipbuilding, primarily structural steel in ship hulls. More precisely, he is manufacturing metal materials for ship structures in accordance with ship construction standards. He primarily produces ship steel plates and structural steel.
At present, we can undertake the production of most types of steel and can produce and process marine steel that does not require specifications according to customer needs in different countries and specifications. The specifications are as follows:
The certifications include China CCS, US ABS, Germany GL, France BV, Norway DNV, Japan KDK, and UK LR.
(1) Variety specifications
Based on their minimum yield point, we divide the strength grades of structural steel used in ship hulls into general-strength structural steel and high-strength structural steel.
China Classification Code standards divide the general-strength structural steel into four quality grades: A, B, D, and E. The high-strength structural steel has three strengths and four quality grades:
A32 A36 A40
D32 D36 D40
E32 E36 E40
F32 F36 F40
(2) Mechanical properties and chemical composition
The mechanical properties and chemical composition of general-strength ship structural steel are under investigation.
General strength steel grade yield point σ s (MPa) not less than tensile strength σ b (MPa) elongation rate σ% not less than carbon C manganese Mn silicon Si sulfur S phosphorus P
A 235 400-520 22 ≤0.21 ≥2.5 ≤0.5 ≤0.035 ≤0.035
B≤0.21 ≥0.80 ≤0.35
D≤0.21 ≥0.60 ≤0.35
E≤0.18 ≥0.70 ≤0.35
What are the mechanical properties and chemical make-up of high-strength shipbuilding steel? The yield point (π s) must be at least as high as the tensile strength (π b), and the elongation rate (π%) must be at least 40%.
A32 315 440-570 22≤0.18 >0.9-1.60≤0.50 ≤0.035≤0.035
D32
E32
F36≤0.16 ≤0.025 ≤0.025
A40 390 510-660 20≤0.18≤0.035≤0.035
D40
E40
F40≤0.16 <0.025 ≤0.025
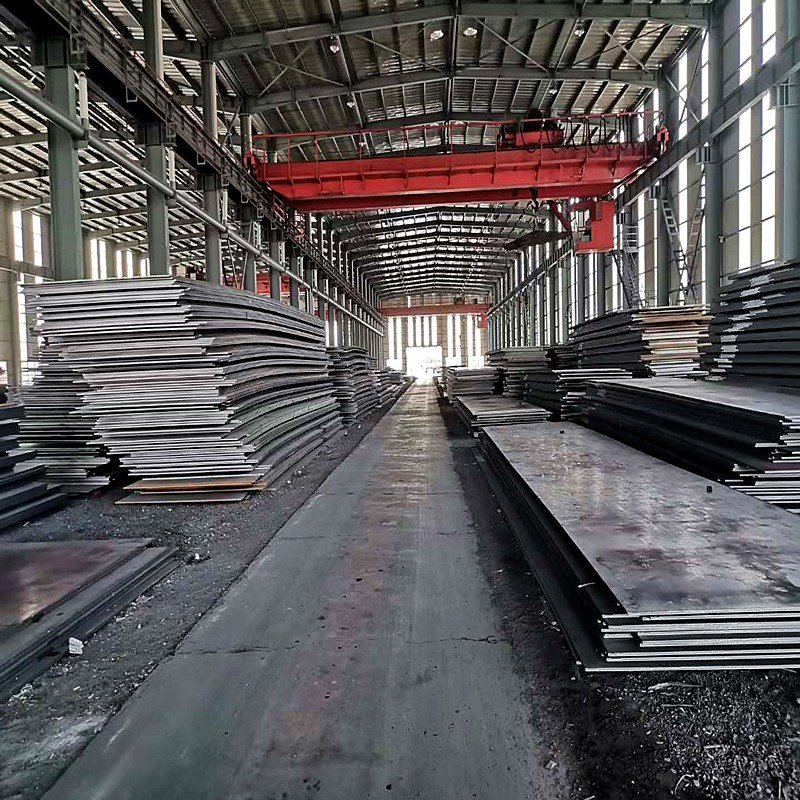
What is a butt welded flange?
The welding flange design is used for butt welding to inclined pipes, forming a very strong connection. These flanges are often used in high-pressure and extreme temperature systems. Docking welding transfers the stress of the flange itself to the connected pipeline. Welded flanges have the following characteristics:
Size and aperture:
The size of the welded flange corresponds to the nominal pipe size of the connected pipeline.
Inner diameter refers to the thickness of the pipe wall. Welded flanges typically come in standard (STD), Schedule 10 (S10), and extra heavy (XH) types.
If a welding neck flange is specified, the size and aperture must match the nominal pipe size and specifications.
Any standard mismatch will alter fluid dynamics and ultimately weaken.
model:
Grade description: The pressure and temperature capacity of the flange. 150 # to 1500 # are the standards for welding neck flanges.
To determine the pressure and temperature requirements of the system.
Shape:
There are two options for welding flanges: convex surface (RF) and flat surface (FF). Face refers to the structure on the back of the flange. The RF flange has a lip inside the bolt ring, while the flat flange, as the name suggests, is completely flat.
If you want to replace the flange in the existing model, you must match the corresponding flange profile. Convex flanges must never be installed on flat flanges.
RF flanges are typically used on pipelines at higher pressures and temperatures.
Material Science:
Welded neck flanges are usually made of carbon steel, but can also be made of stainless steel and aluminum.
When excellent corrosion resistance is required, stainless steel can also be used for production. The welding flange is made of 304L and 316L to improve weldability.
When lightweight products are needed, aluminum products are also an excellent choice.
Gaskets and double headed bolts
Gaskets and bolts are essential accessories for flange installation.
The type of gasket you need depends on the flange surface you choose and the temperature of the environment.
What is a pipeline flange, and how does it work?
Flanges are a reliable method of connecting pipeline systems with various equipment, valves, and almost all other processing system components, and they are the most widely used connection method after welding.
Flanges make it easier to disassemble and improve access to system components, thereby increasing the flexibility of maintaining pipeline systems.
A typical flange connection consists of three parts:
Pipe flange
Gasket
Bolt
In most cases, there are specific gasket and bolt materials that are the same or approved as the pipeline components you want to connect. Stainless steel flanges are one of the most common types of flanges. However, there are many flange materials, so you must match them to your needs.
Other common flange materials include monel alloy, inconel alloy, chromium molybdenum alloy, and many other materials, depending on the application.
The most suitable choice for your needs depends on the system you plan to use with flanges and your specific requirements.
comments