products
- Metal Casting (1)
- Metal Forging (1)
- Metal Laser Cutting (1)
- Metal Molds (1)
- Metal Surface Treatment (1)
- Uncategorized (24)
blogs
- P20 mold steel 2024 年 10 月 30 日
- Shell casting offers a number of important advantages. 2024 年 10 月 30 日
- D2 tool steelPerformance and Application of D2 Tool SteelD2 tool steel 2024 年 10 月 24 日
- Characteristics of AISI 4140 composite steel 2024 年 10 月 22 日
- Characteristics of SAE4340 steel 2024 年 10 月 22 日
Contact us for more information
What is grouting after pouring pile?
Grouting pipe after grouting pile is a pipeline system used for grouting construction after grouting the pile. It consists of grouting pipes and grouting valves, usually made of high-strength materials such as steel pipes or plastic pipes.
After the construction of the grouting pile is complete, the main purpose of the grouting pipe is to inject cement mortar and other materials into the pile body, thereby enhancing the strength and bearing capacity of the pile body. Another function of the grouting pipe is to prevent the leakage of mud and cement mortar inside the pile body, ensuring the smooth progress of grouting construction.
The method for installing and using grouting pipes after grouting piles is as follows:
After the completion of the grout pile construction, insert the grouting pipe into the pile body, and the length of the grouting pipe should be the same as the length of the pile body.
Connect the grouting valve and grout pipe to ensure a secure connection and good sealing.
Inject cement mortar and other materials into the pile body, determining the grouting amount based on the pile body’s size and requirements.
Always monitor the grouting pressure and flow rate during the grouting process to make sure the grouting effect satisfies the requirements.
What are the anti-corrosion techniques for galvanized coatings in sheet metal processing?
The basic sheet metal processing flow for galvanizing (EG) electroplating involves pre-plating the parts, followed by degreasing, erosion, polishing, galvanizing, paint stripping, and passivation/dyeing. When you electroplate something, you can make a dense, uniform galvanized layer with a clean surface, a thin oxide film, more surface activity than phosphating, good flexibility, and high corrosion resistance. The uniformity of coating quality is better than hot-dip galvanizing, but the thickness of coating is not as satisfactory as hot-dip galvanizing. Because of its high surface quality, it is suitable for the exterior panels of passenger car bodies.
(2) The production process for hot-dip galvanizing (GI/GA) used in sheet metal processing is as follows: The process for pre-plated parts includes degreasing, water washing, acid washing, water washing, pressing, solvent coating, drying, galvanizing, cooling, straightening, oiling, and packaging.
In hot dip galvanized iron alloy (GA), the iron in the cold-rolled matrix of GI products diffuses into the zinc layer through the heat treatment process. This creates a zinc iron alloy with about 10% iron that is resistant to corrosion and has a multi-layer phase structure that makes the coating stick better and be easier to weld. After phosphating, the coating surface has excellent corrosion resistance under the film, but there are common pinhole defects.
The flow of sheet metal processing for mechanical galvanizing is described in detail. Different processes mainly involve different methods for establishing the base layer and thickening the coating, which can be roughly divided into two types.
We manufacture metal parts for chemicals, petroleum, or ships.
We are a professional manufacturer of flange forgings, shaft forgings, wheel forgings, gear forgings, and pipeline fittings.
We have many years of experience producing and operating flanges and fittings, and we constantly improve with the tremendous changes in the energy industry to meet the development requirements. No matter how demanding your requirements are, we will promptly respond to your suggestions and link them with production.
We have integrated production capabilities from forging, heat treatment, machining, physical and chemical inspection, surface treatment, packaging, and shipping. We have strong financial strength, solid technical strength, advanced production technology, complete quality inspection, reliable after-sales service, and a solid corporate reputation, providing a solid cooperation foundation for numerous customers around the world and domestically.
Our products are distributed throughout China and around the world, and they are mainly used in the following industries:
<1> The water supply and wastewater treatment system;
<2> Petroleum, chemicals, electric ships, and wind power
<3> Offshore oil fields and gas pipelines
<4> Nuclear energy industry
crude oil transportation
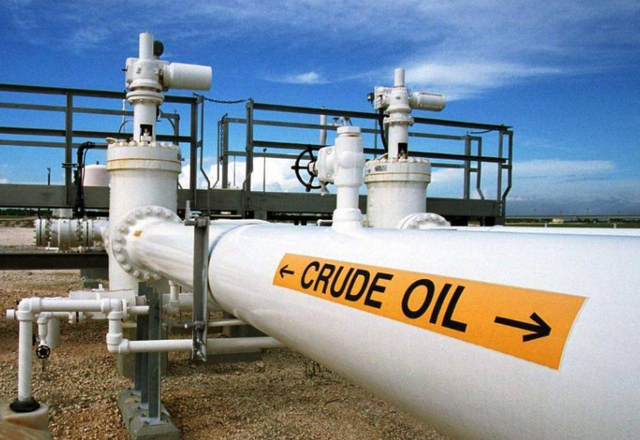
Wind power application

Advantages of Steel Springboards for Construction Ships
Steel gangboards for construction ships have fireproof, sandproof, lightweight, alkali-resistant, high compressive strength, surface concave convex holes, and double-sided I-shaped design effects that are more significant than similar products. The hole spacing is neat, the shape is standardized, it is beautiful, and it is durable (it can be used continuously for 6–8 years under normal construction). The special sand leakage process on the bottom surface plays a role in preventing sand accumulation and is particularly suitable for use in sandblasting workshops in shipyards. By using steel springboards, the number of steel pipes used for scaffolding can be appropriately reduced, thereby improving the efficiency of the installation. Compared to woodblocks, it has a lower price and can still recoup 35%–40% of the investment after many years.
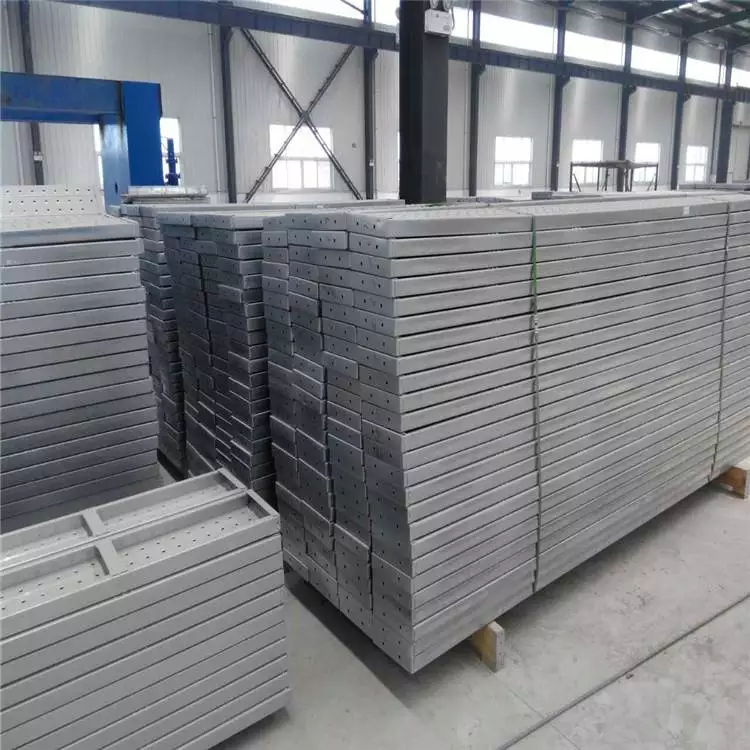
Steel springboard for construction ships
Steel gangboards for construction ships are a type of construction equipment in the construction industry. It can be commonly referred to as steel scaffold board, construction steel springboard, steel pedal, galvanized steel springboard, hot-dip galvanized steel pedal, widely used in industries such as shipbuilding, oil platforms, power, and construction. We use a steel springboard with M18 bolt holes to connect plates and adjust the platform bottom width. BWe use a skirting board with a height of 180 mm between the steel gangways, coat it with black and yellow paint, and secure it with screws in each of the three holes. his method can fix and connect steel springboards together. Following the completion of the wiring, the materials used to construct the platform should undergo strict acceptance checks. Once the platform construction is complete, we should conduct testing. Once we install and hang the equipment, we can use it.
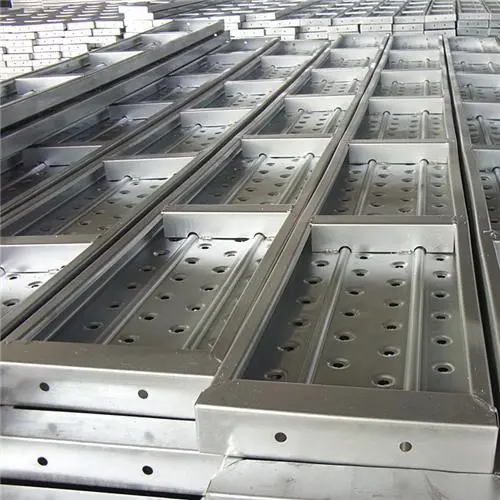
Ships use high-strength low-alloy steel.

Ships have a unique working environment and usage scenarios. Shipboard steel necessitates the inclusion of additional alloying elements in carbon steel products. The addition of alloying elements enhances the strength and resistance to corrosion in metal steel. Our high-strength alloy steel is used in large quantities on current military vessels. Metal connections between the skeleton and various parts primarily utilize our high-strength alloy steel. It can guarantee the hull’s strength and stability.
There are numerous classifications for alloy steel.
Consider materials such as high-strength low-alloy steel. Choose appropriate steel materials based on various environments, functions, and usage methods.
comments