products
- Metal Casting (1)
- Metal Forging (1)
- Metal Laser Cutting (1)
- Metal Molds (1)
- Metal Surface Treatment (1)
- Uncategorized (24)
blogs
- P20 mold steel 2024 年 10 月 30 日
- Shell casting offers a number of important advantages. 2024 年 10 月 30 日
- D2 tool steelPerformance and Application of D2 Tool SteelD2 tool steel 2024 年 10 月 24 日
- Characteristics of AISI 4140 composite steel 2024 年 10 月 22 日
- Characteristics of SAE4340 steel 2024 年 10 月 22 日
Contact us for more information
What is a high-pressure boiler tube?
High-pressure boiler tubes are essential components in industrial production processes, and their material choices are becoming increasingly diverse. The high-pressure boiler tubes we have launched are a product with excellent performance.
Our products are mainly used for manufacturing high-pressure boilers, and the advantages of our high-pressure boiler tubes mainly lie in their high temperature resistance and corrosion resistance. It can also withstand a lot of pressure. It is an ideal pipe material for high-pressure boilers.

Our products are mainly used in pipelines for industries such as boilers, gas transportation, liquid transportation, chemical pipelines, electricity, metallurgy, ships, machinery, etc.
Die casting molds are used to produce automotive oil pans
Our company produces die-casting molds for automotive oil pans, including upper and lower molds. An upper mold equips the upper end of the lower mold, and we install the upper and lower mold cores between them to ensure their cooperation. A long convex platform arranges itself in the middle of the upper end face of the lower mold core. The length of the convex platform’s front and rear end faces is greater than that of the left and right sides. The convex platform features a large insert block on its left side and a diversion cone and small insert block on its rear. Several inner runners connect the diversion cone to the convex platform. The exhaust groove connects to several overflow grooves arranged on the right side of the convex platform, while the exhaust valve connects to several overflow grooves arranged in front of the convex platform. This utility model opts to set the inner runner in The utility model minimizes the flow of molten metal on one side of the product coloring surface to reduce pressure loss; The design incorporates multiple internal runners, arranged at intervals to avoid product holes and prevent slag collection and erosion of the product threads. Ensure good slag collection and exhaust of the mold through the exhaust valve and overflow groove.
What are the classifications of stainless steel pipes?
- We follow the
(a) The classification of production methods can be divided into seamless pipes and welded pipes. Seamless tubes are composed of cold-drawn tubes, extruded tubes, and cold-drawn tubes.
(b) According to the production process classification, it can be divided into gas-shielded welded pipes, arc-welded pipes, and resistance-welded pipes. Resistance-welded pipes are divided into two types: high-frequency welding and low-frequency welding.
(c) Additionally, we can classify straight seam welded pipes and spiral welded pipes based on the weld seam.
- We can also classify circular steel pipes and rectangular steel pipes according to their cross-sectional shapes.
- We can also classify according to wall thickness, which can be divided into thin-walled stainless steel pipes and thick-walled stainless steel pipes.
- Simultaneously, we can divide the usage.
Civilian types include round, rectangular, and floral tubes. Civil use is generally used for decoration, construction in progress, building structures, etc.
(b) We can divide the types of industry into several categories, such as stainless steel pipes for industrial engineering, general piping (drinking water), pipes for mechanical structures, fluid velocity delivery pipes, boiler heat exchange pipes, boiler low pressure, medium pressure, high pressure pipes, and food hygiene pipes, among others.
What is the difference between forgings and raw materials such as machined bars and plates?
Forged parts can more easily produce and process casts of twisted metal of various sizes and materials.
Due to limitations in the shape and size of finished materials, such as steel bars and plates, Our forging process may involve processing twisted metal.
This is the only solution for the product.
Forged products can be quickly produced in various shapes and sizes according to our needs. We can produce products with parts as small as 1 inch and as large as over 220000 pounds.
Forging a cast of twisted metal can save more material.
For example, we consider flame-cutting boards to be a highly wasteful process. However, it is an important step in manufacturing metal products, and subsequent processing will result in the loss of more raw materials.
However, the cast of twisted metal waste produced by the forging process is very small, and our forging production efficiency is also very high.
In mass production, our forging process has a significant cost advantage.
cast of twisted metal
What are the products made from aluminum die-casting material?
Commonly used alloys: Aluminum is a highly diversified metal with multiple alloys, each with its own material properties and unique applications. The most common aluminum alloys and their respective chemical compositions are as follows:
A380 is one of the most widely used alloys.
The A360 bears resemblance to the A380, yet it incorporates more silicon and less injected copper.
The B390 has excellent hardware and wear resistance.
A413 is highly processable, has good thermal conductivity, and has the characteristics and applications of conductive alloys.
Each type of aluminum alloy is a unique material with characteristics that make it suitable for different application scenarios. For example:
Because it is lightweight and widely used, A380 aluminum is perfect for manufacturing industrial machinery, industrial components, and consumer electronics products.
A360 aluminum has stronger corrosion resistance and higher temperature strength, making it an ideal choice for ships or hydraulic components.
B390 aluminum is a “hypereutectic” material, mainly due to a silicon content exceeding 13%. It has additional hardness and higher wear resistance, making it an ideal choice for applications in the automotive field such as engine cylinders, powertrain components, and heat exchangers.
Electrical and telecommunications components frequently use A413 aluminum due to its exceptional workability and strength.
Our process for producing flanges
Our current production process for flanges mainly includes casting, forging, die forging, cutting, and other methods.
The production process for casting flanges is to melt the steel in a medium-frequency electric furnace to a temperature of 1600–1700 °C and then preheat the metal mold to 800-900 °C to maintain a constant temperature. Next, inject the molten steel into the preheated metal mold and wait for the casting flange to naturally cool to 800-900 °C for 1–10 minutes. Finally, cool it with water to nearly room temperature and remove the casting from the mold.
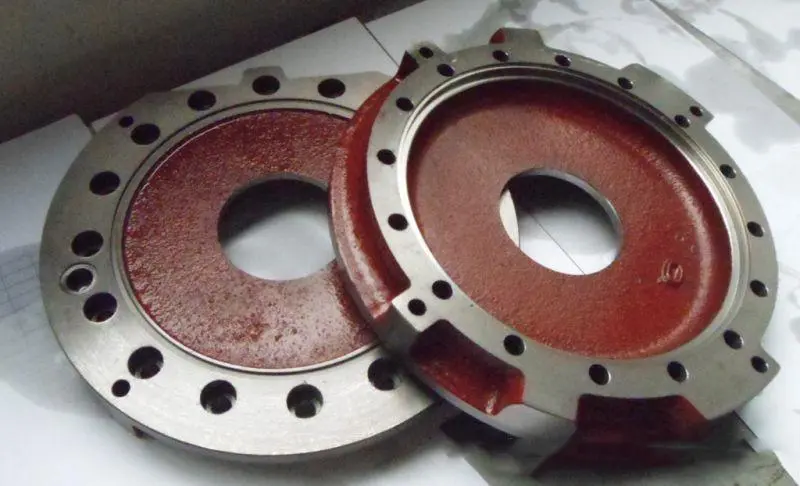
The production process of forging flanges involves the basic steps of selecting high-quality steel billets for cutting, heating, forming, and cooling after forging. The forging methods include free forging, die forging, and membrane forging. Among them are the high dimensional accuracy of the forged parts, the small machining allowance, and the more reasonable fiber structure distribution of the forged parts, which can further improve the parts’ service life.

Our company’s flange production process has its own characteristics, and how to choose the appropriate production process depends on the specific application requirements and product cost considerations. For example, the cost of casting flanges is relatively low, but there may be casting defects. For example, forging flanges have better shape and performance, but the cost is higher. Another advantage is that forged flanges have high precision and excellent performance, but the production process is relatively complex, and the production time may be longer. Large flanges, capable of producing a wider diameter range, typically employ cutting flanges in their production.
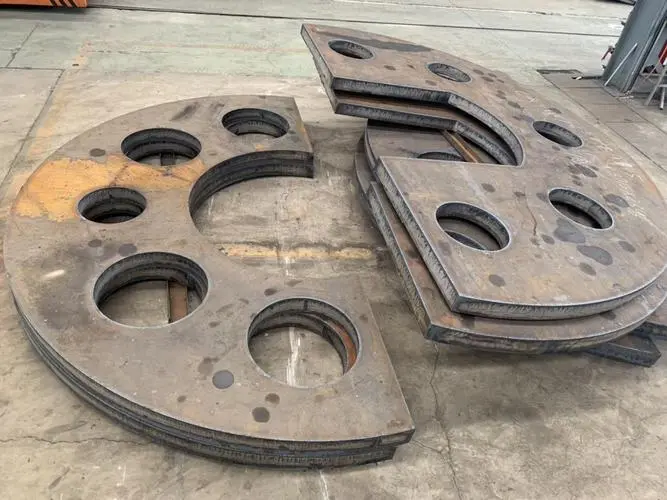
comments